X-48-1800
Cold-blend modifier for acrylic resins
Required Performance | Heat ResistanceWeather ResistanceAlkali Resistance |
---|---|
Features and Applications | Cold BlendableCoating AgentPaints |
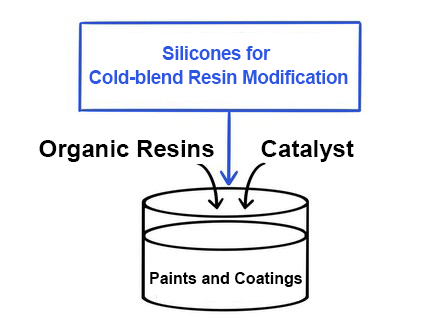
- This product can be used by simply cold-blend*.
- Applicable organic resins are silicone-modified acrylic polymers/polyesters/alkyds/weak solvent acrylic resins/NAD.
- This product improves weather resistance, heat resistance, anti-marking pen fouling properties, acid/alkali resistance, etc..
- Recommended additive amount is 10~50 parts per 100 parts resin solid content.
* Cold blend: A method of blending by simply mixing without heating
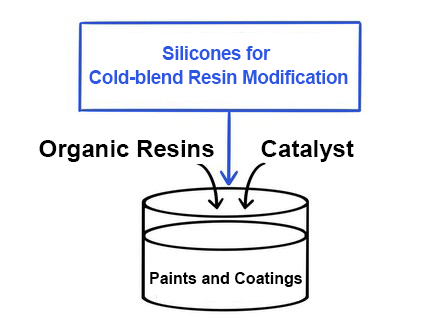
Product Information
X-48-1800 is a silicone oligomer for cold blending with acrylic resins.
X-48-1800 can be cold blended with silicone modified acrylic polymers to further improve the silicone concentration in the coating.
The addition of X-48-1800 improves various coating performances, especially weatherability, heat resistance, and anti-marking pen fouling properties.
The recommended additive amount is 10 to 50 parts by weight for 100 parts by weight of the base acrylic resin. For details, please refer to the paint formulation examples.
The applicable resins are silicone-modified acrylic polymers, polyesters, and alkyds.
It can be applied to room temperature curing and forced drying paints for metals, woods and plastics.
And it can also be applied to inks and other coatings.
Frequently Asked Questions about X-48-1800
Paint Formulation Example
Mill Base Process (PWC* : 70%)
Formulation | Content | Formulation amount (parts) |
---|---|---|
Acrylic silicone polymer |
Made by Kaneka Corporation ZEMLAC AM-1532 |
60 |
Titanium dioxide white pigment | Made by Ishihara Sangyo Co. TIPAQUE CR-90 |
70 |
Dilution solvent | Thinner | 10 |
*PWC : Pigment Weight Concentration
Pigmentation Process
Formulation | Content | Blank | X-48-1800 (30%) |
---|---|---|---|
Mill base | Mill base above | 70 | 70 |
Acrylic silicone-based polymer | ZEMLAC YC-5920 (NV.50%) | 100 | 60 |
Silicone oligomer | X-48-1800 made by Shin-Etsu Chemical Co., Ltd. | – | 20 |
Curing agent for ZEMLAC | BT-120S* made by Kaneka Corporation | 20 | 20 |
Leveling agent | Leveling Agent A made by Shin-Etsu Chemical Co., Ltd. | 0.2 | 0.2 |
Dilution solvent | Thinner | 10 | 10 |
Total | 200 | 180 | |
PWC (pigment weight concentration) % | 35 | 35 | |
Acrylic/X-48-1800 (solids weight) | 100/0 | 70/30 |
*Other catalysts (e.g. organotin-based) can also be used.
Characteristics of the Cured Coating Films
Curing conditions: room temperature x 1 week, film thickness 30 μm
Item | Blank | X-48-1800(30%) |
---|---|---|
PWC(Pigment Weight Concentration)% | 35 | 35 |
■Mechanical properties | ||
Gloss 60° *1 | 90 | 90 |
Pencil hardness *2 | 2H | 2H |
Adhesion (grid test) polished steel plate *2 | 100 / 100 | 100 / 100 |
Impact resistance 500g・cm *2 | 15 | 15 |
Flexibility mm *2 | 10< | 10< |
■Warm water resistance 40°C x 5days *1 | ||
Appearance | Excellent | Excellent |
■Oil repellency 23°C×3h *1 | ||
Red | Good | Excellent |
Blue | Good | Excellent |
Black | Good | Excellent |
■Acid and alkali resistance 23°C×5days *1 | ||
5% NaOH | Poor | Excellent |
5% HCl | Poor | Excellent |
■Heat resistance 200°C×4h. *1 | ||
Gloss retention ratio % 60° | 84 | 88 |
Yellowing degree(ΔYI) | 17 | 12 |
■Weather resistance SUV 30 cycle *3 | ||
Gloss retention ratio % | 70(Cracking) | 70 |
Xenon weather meter(500 h) | 80(Peeling) | 90 |
*1: Schott D263 glass sheet, *2: JIS,G,3141(SPCC-SD)PB-N144 zinc phosphate treated steel sheet, *3: Polyester coated steel sheet
Acid and Alkali Resistance Test
A spot test was conducted using a 5% hydrochloric acid solution and a 5% NaOH solution.
The appearance of the films was visually evaluated after standing for 5 days respectively.
It can be seen that the addition of X-48-1800 improves both the acid resistance and alkali resistance.
Formulation: P.W.C 35% (CR-90), Coating: film thickness 30μm, Substrate: glass
Anti-marking Pen Fouling Properties
After drawing a line with an oil-based pen and leaving it for 3 hours, the stain was removed with
Then, we evaluated whether it can be wiped off with Bencot M-3II (Asahi Kasei Corporation) soaked in a mixture of ethanol and toluene (1:1). The results were evaluated to see if they could be wiped off.
It can be seen that the addition of X-48-1800 sufficiently wipes off the ink compared to the blank.
Formulation: P.W.C 35% (CR-90), Coating: Film thickness 30μm, Substrate: Glass
Heat Resistance
Heat resistance tests were conducted under heating conditions of 200°C.
The film thickness was approximately 30 μm, and a glass plate was used as the test specimen, and the gloss and color difference at each heating time were evaluated.
It can be seen that the addition of X-48-1800 increases the gloss retention rate and suppresses yellowing.
Formulation: P.W.C. 35% (CR-90), Coating: Film thickness 30μm, Substrate: Glass, Temperature: 200°C
Coating Film Appearance after 200°C x 20 Hours
Weather Resistance
Accelerated weathering tests were conducted using a super accelerated weathering tester (Eye Super UV Tester SUV-W151 made by Iwasaki Electric Co., Ltd.) and a xenon weather meter (Q-SUN Xe-3 Xenon Test Chamber made by Q-Lab. Corporation).
After each accelerated test, the gloss and appearance of the coating film were evaluated.
It can be seen that the addition of X-48-1800 increases the gloss retention rate and suppresses cracking and flaking.
SUV Test (10cycle = 1 Year Equivalent)
Thickness: 30 μm, Substrate: Polyester coated steel sheet
*1 cycle: UV (90mW) irradiation for 4 hours → dark for 4 hours → condensation for 4 hours
Xenon Weather Meter Test (Equivalent to 1000h=1 Year)
Gloss retention ratio % | |
---|---|
X-48-1800(30%) | 90 |
Blank | 80 |
Thickness: 30μm, Substrate: Polyester coated steel sheet
Xenon weather meter 500h later
*1h (irradiation) -> 1h (condensation/irradiation) -> 1h (condensation)
Thickness: 30μm, Substrate: polyester coated steel plate, Appearance after 1000h in xenon weather meter
Frequently Asked Questions
Question: About X-48-1800 | Answer |
---|---|
1.What is X-48-1800? | It is a silicone oligomer with excellent compatibility with organic resins and reactivity in resins. |
2.How to use? | Cold blending will modify the resin. It is especially effective for silicone modified resins. We recommend cold blending with silicone-modified acrylic resins as shown in the Paint Formulation Example on this webpage. |
3.What is the curing mechanism? | A hydrolysis reaction with the alkoxysilane in the acrylic resin forms a siloxane bond. |
4.What should I pay attention to when blending? | Make sure that the product is compatible with the resin. If the paint film becomes slightly cloudy or whitish, it will be difficult to get good performance. |
5.Does it have water repellency? | It is slightly inferior to silicone fluid, but it will maintain its water repellency. |
6.What if the water repellency is insufficient? | It is possible to improve the water repellency by adding 1000ppm to several percent of carbinol-modified fluorine-containing silicone(i.e. X-48-7014), or modified silicone fluid. |
7.What should I do for the actual formulation? | Please refer to the Paint Formulation Example on this web page. |
8.What is the storage stability of X-48-1800? |
Seal container tightly and store in a cool, dark place (25℃ or below, out of direct sunlight) with good ventilation. Keep away from heat and flame. After use, be sure to seal tightly to prevent moisture and humidity from entering the product. |
Question: About compatibility | Answer |
1.What are the acrylic resins that are easily compatible? | Silicone modified resins are easily compatible with each other. Even unmodified resins can be used to the extent that they are compatible. |
2.What is the compatibility with resins other than acrylics? | Silicone modified resins such as silicone modified alkyd resins and silicone modified polyester resins are more compatible. The same effect can be expected with unmodified silicone resins if they are compatible. |
Question: About compounding | Answer |
1.What kind of resin do you recommend to use for mill base (MB)? | The Gemlac AM-1532 (made by Kaneka corporation) which is a pigment dispersion resin is recommended. Also, any other resins with good dispersibility can be used. |
2.In the example of paint formulation, pigments are used, but what is the recommended formulation for clear paints? | Mix resin/X-48-1800 (solids weight ratio) = 70/30, add reaction catalyst and leveling agent if necessary. For the reaction catalyst, a general condensation curing catalyst (e.g. organotin) can be added at 0.05-2% to provide good curing properties. |
3.Is it possible to increase the dosage of X-48-1800? | If it is compatible, it is possible. |
4.What will be changed by increasing X-48-1800? | The more it is increased, the better the weatherability, heat resistance and anti-marking pen fouling properties. |
5.What is the minimum amount of X-48-1800 that will be effective? | The minimum amount is about resin/X-48-1800 (solids weight ratio) = 80/20. It depends on the type and structure of the resin. |
6.What is the recommended dilution solvent? | Single or multiple mixed solvents such as butyl acetate, ethyl acetate, MEK, MIBK, toluene, xylene, and alcohols. |
7. Does it need a catalyst? | Yes, it is necessary. |
8.Which catalyst can be recommended except organo-tin catalyst ? | DX-9740 (aluminum catalyst made by Shin-Etsu Chemical Co., Ltd.), etc. |
9.What is the stability of the blended paint? | If the catalyst is not included, it is relatively stable. Also, depending on the type of resin, it can be applied within a day or two after the catalyst is added. |
Question: About coating | Answer |
1.What are the drying conditions? | Dry at room temperature (20℃~25℃) for 1 week. Or, forced drying (80℃ x 20 minutes) + 1 day of drying at room temperature is the guideline. |
2.What if uncured components remain on the surface of the cured film? | It is possible that the catalyst amount is too high. The problem may be solved by examining the amount of catalyst. In addition, forced drying by heating is likely to cause this kind of issue, and it may be solved by using room temperature curing. |
3.Which coating methods are possible? | You can follow the normal coating methods such as spray, roll coater, flow coater, etc. |
4.What are the precautions for paint storage? | Please refer to answer 8 about X-48-1800 |
5.What is the film thickness? | Not specific, but in the range 5μm to 100μm. |
6.What substrates can be coated? | Metals, non-ferrous metals, glass, inorganic materials, plastics, and wood. The surface of the substrate should be degreased or otherwise cleaned before application. |
Question: About the application | Answer |
What are the expected uses? | ・Top coat for woods ・Top coat for plastics ・Topcoat for inorganic construction materials ・Elastic top coat ・Topcoat for waterproof materials ・Top coat for metals (iron, aluminum, stainless steel) ・Primer for photocatalytic layer |
Applicable solvent type | Organic solvent type |
---|---|
Applicable resin | Silicone modified resin |
Solvent type | Solvent-free |
Usage | Additive |
Appearance | Colorless transparent |
Active ingredient (%) | 100 |
Viscosity at 25℃ | 100 mm2/s |
Specific gravity at 25℃ | 1.16 |
Refractive index at 25°C | 1.51 |
UN Number | N/A |
Packaging | 100g(sample only),1㎏ |
(Not specified values)
Product Inquiry
X-48-1800
Inquiry FormRelated Material
Related Product List
Product Name | Type | Cure Method | Solvent System | Usage | Film Hardness | Common Name | Brief Description |
---|---|---|---|---|---|---|---|
KC-89S | Type A | Room Temperature Cure | Solvent-free (100% Silicone Content) | Main Agent, Resin Modifier | High | Low degree of polymerization methyl oligomer | ・Low molecular weight ・It consists of only T unit. ・It forms high hard film. ・It has been used as binders of coatings. |
KR-515 | Type A | Room Temperature Cure | Solvent-free (100% Silicone Content) | Main Agent, Resin Modifier | Medium | Medium degree of polymerization methyl oligomer | ・Higher molecular weight than KC-89S. ・It consists of only T unit. ・It has been used as binders of coatings and organic resin modifiers. |
KR-500 | Type A | Room Temperature Cure | Solvent-free (100% Silicone Content) | Main Agent, Resin Modifier | Medium | Medium degree of polymerization methyl oligomer | ・Higher molecular weight than KC-89S. ・It consists of only T unit. ・It is a standard product of methyl type. ・It has been used as binders of coatings and organic resin modifiers. |
X-40-9225 | Type A | Room Temperature Cure | Solvent-free (100% Silicone Content) | Main Agent, Resin Modifier | Low | High degree of polymerization methyl oligomer | ・Higher molecular weight than KR-500. ・It consists of only T unit. ・It has been used as binders of coatings and organic resin modifiers. |
X-40-9246 | Type A | Room Temperature Cure | Solvent-free (100% Silicone Content) | Main Agent, Resin Modifier | Low | High degree of polymerization methyl oligomer | ・D unit is introduced to impart flexibility. ・It has been used as binders of coatings and organic resin modifiers. |
X-40-9250 | Type A | Room Temperature Cure | Solvent-free (100% Silicone Content) | Main Agent, Resin Modifier | Low | High degree of polymerization methyl oligomer | ・D unit is introduced to impart flexibility. ・It has been used as binders of coatings and organic resin modifiers. |
X-88-1004 | Type A | Room Temperature Cure | Solvent-free (100% Silicone Content) | Main Agent, Resin Modifier | High | High adhesion, high hardness oligomer | ・Excellent adhesion to hard-to-bond substrates such as SUS and acrylic ・High hardness and excellent scratch resistance. |
X-88-1007 | Type A | Room Temperature Cure | Solvent-free (100% Silicone Content) | Main Agent, Resin Modifier | Low | High adhesion, crack resistant oligomer | ・Excellent adhesion to hard-to-bond substrates such as SUS and acrylic ・Excellent crack resistance and water repellency |
KR-400N | Type A | Room Temperature Cure | Solvent-free (100% Silicone Content) | Main Agent, Resin Modifier | High | High hardness methyl oligomer | ・It forms high hard coatings. ・This products is a KR-400 without the curing catalyst. |
X-48-1500 | Type A | Room Temperature Cure | Solvent-free (100% Silicone Content) | Main Agent, Resin Modifier | – | Flex resistant oligomer | ・It combines high hardness and flex resistance. ・Rapid cure |
X-48-1501 | Type A | Room Temperature Cure | Solvent-free (100% Silicone Content) | Main Agent, Resin Modifier | High | High hardness, flex resistance, heat crack resistance, impact resistance oligomer | ・It forms a film with high hardness, flex resistance heat resistant crack resistance and impact resistance. |
X-48-1600 | Type A | Room Temperature Cure | Solvent-free (100% Silicone Content) | Main Agent, Resin Modifier | – | Ethoxy type, flex resistant oligomer | ・It combines high hardness and flex resistance. ・It cures by deethanol reaction of ethoxy groups. ・Environmentally friendly type (because it is not a demethanol reaction) |
KR-401N | Type A | Room Temperature Cure | Solvent-free (100% Silicone Content) | Main Agent, Resin Modifier | Medium | Flex resistance, Methyl / Phenyl type oligomer | ・It forms a flexible film. ・High gloss ・This products is a KR-401N without the curing catalyst. |
KR-510 | Type A | Room Temperature Cure | Solvent-free (100% Silicone Content) | Main Agent, Resin Modifier | – | Methyl / Phenyl type oligomer for resin modificatioon | ・It is a standard product of methyl / phenyl type. ・It has been mainly used as modification of heat resistance and weatherability of organic resin. ・It imparts flexibility and crack resistance to oligomer type coating agents. |
KR-213 | Type A | Room Temperature Cure | Solvent-free (100% Silicone Content) | Main Agent, Resin Modifier | – | Methyl / Phenyl type oligomer for resin modificatioon | ・For resin modification ・It imparts flexibility and crack resistance. |
X-40-9312 | Type A | Room Temperature Cure | Solvent-free (100% Silicone Content) | Main Agent, Resin Modifier | High | High hardness, flex resistant oligomer | ・It has high hardness and crack resistance. ・Excellent yellowing resistance and crack resistance after light irradiation |
KR-400 | Type A | Room Temperature Cure | Solvent-free (100% Silicone Content) | Main Agent | High | One-component cure high hard oligomer | ・It is a standard product of one-component (containing catalyst) type ・It forms high hard film. |
X-40-2327 | Type A | Room Temperature Cure | Solvent-free (100% Silicone Content) | Main Agent | Medium | One-component rapid cure oligomer | ・Rapid cure |
KR-401 | Type A | Room Temperature Cure | Solvent-free (100% Silicone Content) | Main Agent | Medium | One-component cure flex resistant oligomer | ・Excellent flex resistance ・High gloss |
KR-4000G | Type A | Room Temperature Cure | Organic Solvent | Main Agent | Low | One-component cure high gloss oligomer | ・Excellent gloss ・Excellent water repellency and water sliding property. ・It exhibits antifouling properties even after wiping up applications. |
X-40-2450 | Type A | Incurable (For Resin Modification) | Solvent-free (100% Silicone Content) | Resin Modifier | – | Ionic liquid modified oligomer | ・Easy to migrate to the surface when added to resin ・It provides antistatic properties with a small amount of addition. ・It has releasability. |
X-40-9300 | Type A | Room Temperature Cure | Solvent-free (100% Silicone Content) | Main agent, Resin Modifier | Alkary resistant rapid cure oligomer | ・Rapid curing due to extremely high reactivity of alkoxy groups ・Alkali resistance ・Water resistance |
|
X-40-9301 | Type A | Room Temperature Cure | Solvent-free (100% Silicone Content) | Main agent, Resin Modifier | Alkary resistant oligomer | ・Alkali resistance ・Water resistance |
|
KR-517 | Type AR | Incurable | Solvent-free (100% Silicone Content) | Resin Modifier | – | Epoxy group containing oligomer | ・Alkoxy groups are methoxy groups and ethoxy groups. ・Epoxy equivalent 830g/mol |
X-24-9590 | Type AR | Incurable | Solvent-free (100% Silicone Content) | Resin Modifier | – | Epoxy group containing oligomer | ・Alkoxy groups are methoxy groups. ・Epoxy equivalent 590g/mol |
KR-516 | Type AR | Incurable | Solvent-free (100% Silicone Content) | Resin Modifier | – | Epoxy group containing oligomer | ・Alkoxy groups are methoxy groups. ・Organic functional groups have methyl groups in addition to epoxy groups. ・Epoxy equivalent 280g/mol |
KR-518 | Type AR | Incurable | Solvent-free (100% Silicone Content) | Resin Modifier | – | Mercapto group containing oligomer | ・Alkoxy groups are methoxy groups and ethoxy groups. ・Mercapto equivalent 800g/mol |
KR-519 | Type AR | Incurable | Solvent-free (100% Silicone Content) | Resin Modifier | – | Mercapto group containing oligomer | ・Alkoxy groups are methoxy groups. ・Organic functional groups have methyl groups in addition to mercapto groups. ・Mercapto equivalent 450g/mol |
KR-513 | Type AR | Incurable | Solvent-free (100% Silicone Content) | Resin Modifier | – | Acrylic group containing oligomer | ・Alkoxy groups are methoxy groups. ・Acrylic equivalent 210g/mol |
X-40-9296 | Type AR | Incurable | Solvent-free (100% Silicone Content) | Resin Modifier | – | Methacrylic group containing oligomer | ・Alkoxy groups are methoxy groups. ・Methacrylic equivalent 230g/mol |
KR-511 | Type AR | Incurable | Solvent-free (100% Silicone Content) | Resin Modifier | – | Vinyl group containing oligomer | ・Alkoxy groups are methoxy groups. ・Vinyl equivalent 530g/mol |
KR-470 | Type R | Heat Cure, UV cure | Solvent-free (100% Silicone Content) | Main Agent, Resin Modifier | High | Cyclic siloxane tetrafunctional oligomer containing alicyclic epoxy group | ・Relatively low molecular weight and excellent compatibility with epoxy resins ・It has a cyclic siloxane back bone and shrinkage is small during curing. |
X-40-2678 | Type R | Heat Cure, UV cure | Solvent-free (100% Silicone Content) | Main Agent, Resin Modifier | Medium | Cyclic siloxane bifunctional oligomer containing alicyclic epoxy group | ・Relatively low molecular weight and excellent compatibility with epoxy resins ・It has a cyclic siloxane back bone and shrinkage is small during curing. ・Excellent crack resistance due to bifunctionality |
X-40-2669 | Type R | Heat Cure, UV cure | Solvent-free (100% Silicone Content) | Main Agent, Resin Modifier | – | Linear siloxane bifunctional oligomer containing alicyclic epoxy group | ・Relatively low molecular weight and excellent compatibility with epoxy resins ・With straight-chain siloxane back bone, good leveling property and wettability ・Low viscosity and effective as a reactive diluent |
X-40-2728 | Type R | Heat Cure, UV cure | Solvent-free (100% Silicone Content) | Main Agent, Resin Modifier | Medium | Glycidyl group containing cyclic siloxane bifunctional oligomer | ・Relatively low molecular weight and excellent compatibility with epoxy resins ・ It has a cyclic siloxane back bone and shrinkage is small during curing. ・Excellent crack resistance due to bifunctionality |
X-40-2761 | Type R | UV Cure | Solvent-free (100% Silicone Content) | Main Agent, Resin Modifier | – | Acrylic group containing flex resistant oligomer | ・It imparts crack resistance. ・Excellent compatibility with acrylates and various photo initiators |
KR-2710 | Type R | Incurable | Solvent-free | Resin Modifier | – | Polycarbonate flame retardant | ・Polycarbonate flame retardant ・Excellent transparency |
X-48-1800 | – | Incurable | Solvent-free | Resin Modifier | – | Silicone for cold blend resin modification | ・Cold blend resin modifier for silane modified acrylic resin ・Improving weatherability, heat resistance, magic marker stain resistance and acid and alkali resistance ・Recommended addition amount = 10 to 50 parts per 100 resin solid content |
X-48-1801 | – | Incurable | Solvent-free | Resin Modifier | – | Silicone for cold blend resin modification | ・Cold blend resin modifier for isocyanate curing resin ・Improving weatherability, magic marker stain resistance ・Recommended additive amount = 3% to 20% (converted to NCO equivalent) to curing agent |
X-48-5030 | Type R | UV Cure | Solvent-free (100% Silicone Content) | Main Agent | High | Solvent-free UV cure hard coating agent | ・Excellent low viscosity, scratch resistance, and low warpage |
X-48-5031 | Type R | UV Cure | Solvent-free (100% Silicone Content) | Main Agent | High | Solvent-free UV cure hard coating agent | ・Excellent weatherability, low viscosity, scratch resistance and low warpage. |
X-88-2003A | Type A | Room Temperature Cure | Solvent-free (100% Silicone Content) | Main Agent | High | High hard, crack resistant, anti-fouling coating agent | ・It has high hardness and crack shrinkage property (Water repellency, water sliding property, magic marker stain resistance) ・One-component rapid cure type |